Careers Series: Iain Walker - Operations Manager
- Iain Walker
- Oct 15, 2018
- 5 min read
The latest guest blog for Girl On a Building Site is by Iain Walker. Ian is an Operations Manager at G&E Facilities where he works to ensure the business grows in a sustainable and successful way. Below he shares his career journey which demonstrates how many opportunities the Construction Industry can provide.
How I got into Construction
When I left sixth-form college, I still had no real idea what I wanted to do for a job, in fact the whole idea of working from 9 to 5, 5 days a week for 50 years depressed me. However, I had been told to find something I like and that seemed like good advice, so I looked for jobs that involved drawing.
In my local paper I found a small advert for Technical Apprentices with Crown House Engineering in the construction industry and applied, along with a few others, without any real expectation of being successful or even being sure that was a job I wanted. I applied because the advert listed ‘technical drawing’ as one of part of the role I would learn and because I’d been told apprenticeships were a good thing.
When I received by post an invitation to an interview, I was both surprised and excited (at last). I was fortunate to be one of two office-based apprentices taken on that year.
Day to day job
In fact, I found that over the next 4 years I learnt a lot about pipe-fittings, filing, specifications, driving company cars, collecting materials, dealing with all sorts of people, making tea and not much about the actual production of technical drawings, but plenty of about making minor modifications and printing other people’s drawings. At that time, drawings were done by hand, typically on A1 or A0 film which could be updated or changed by scraping the top layer of film off and re-applying the ink (preferably without smudging or letting the ink bleed). Printing the drawings involved use of a large ammonia-based copy machine, which stank, and a lot of folding, filling out of Drawing Issue Sheets and often driving them to site too.
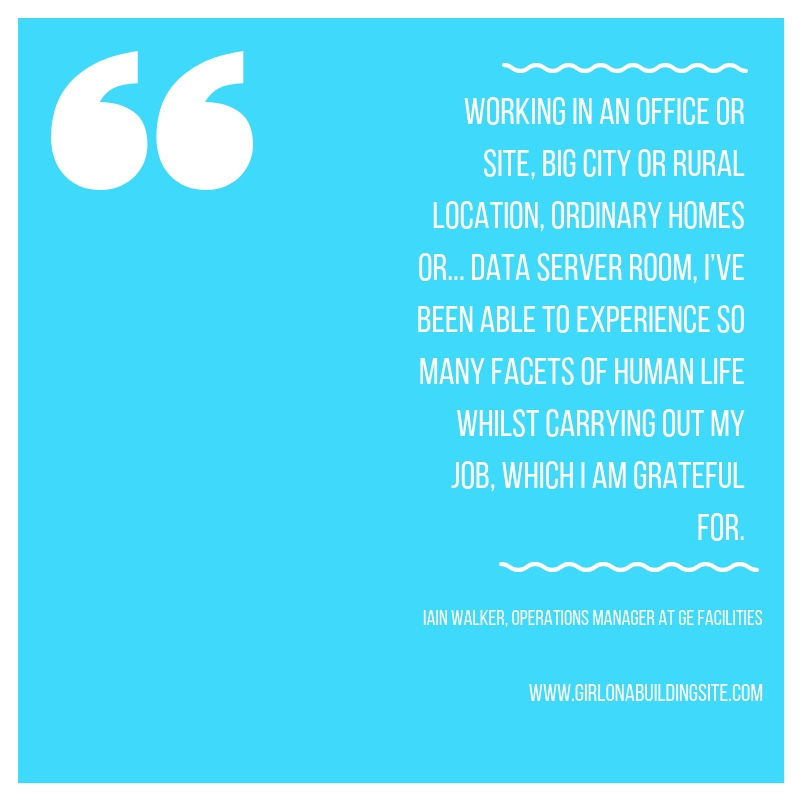
I also attended college on day release, 8am to 8pm, for 4 years. The college struggled to resource teaching staff for the course and the other students came from quite varied backgrounds and experience, and I often wondered when I was ever going to apply what I was learning at college to my ‘normal’ day at work. This mostly consisted of assisting Contracts Engineers running multiple projects and Estimators making list of pipe and fittings from drawings, then entering it into the computer database. College was all about learning the theory behind designing Heating, Ventilating and Air-conditioning systems, using calculators and forms, when even then we all knew that computers could do it faster and easier. In hind-sight, if we had got 2 years experience before starting those modules, they would’ve been a lot more relevant to our daily activities and therefore been much more interesting too.
Whilst an apprentice, I learnt that I enjoyed the team effort involved in larger building contracts, as Crown House Engineering directly-employed pipefitters and plumbers, with traditional Foremen and Charge-hands too. My role was usually the organiser and co-ordinator of pipe-fittings, radiators, grilles, etc, including raising Requisitions for them. Also cross-checking specifications and drawings against actual installations, raising Technical Queries and logging the issue and receipt of drawings, and lots of filing. Then as projects neared completion I would update the drawings to include the changes inevitably made during construction and produce draft Operating and Maintenance Manuals
Later, as I became more experienced, I attended site meetings, met clients, set the site teams to work and made sure they kept to the plan. Then, starting with smaller projects, I was trusted to run my own projects, but under the guidance of a more senior Engineer.
Best and Worst things
I have always been a bit of know-it-all and I found I also like to be in charge, so the project management, and later business management, aspects of the job have turned out to be the parts of the job that I actually prefer. Efficiency and organisation have been the key to success as a construction professional and those disciplines have stayed with me, but also been supplemented with listening skills, which are great for sales and leadership. I’ve also always enjoyed the variety that working in the construction industry provides. Working in an office or site, big city or rural location, ordinary homes or highly restricted areas, call centre or data server room, I’ve been able to experience so many facets of human life whilst carrying out my job, which I am grateful for.
The most frustrating parts of the job have always been other the people who are aren’t trying to deliver a successful project. Sometimes that’s been due to lack of motivation, sometimes over-inflated egos but mostly it seems it’s an attempt to become rich at other people’s cost. Unfortunately, being a sub-contractor means that you’re always at risk of taken advantage of by the people higher in the chain (the main contractor or client) and often there is very little that you can do about it.

Changes in direction
I have never been out of work during my 30 year career in construction but I have changed ‘direction’ quite a lot. The first 10 years was mostly gaining experience and chasing a higher salary, which was reasonably easy to do as Mechanical Contracts Engineers were in high demand and low supply after the 1990 recession which caused a cut-back on training new staff throughout the industry.
In an effort to avoid some of the frustrations mentioned above, I tried side-stepping into project management for an air-conditioning system manufacturing company, which got me onto some of the highest rooftops in London. Next I accepted an offer to be Operations Manager for a small company providing specialised services assisting the larger Facility Management companies, which gave me interesting insight into how large corporations operate, like IBM and BskyB, also government operations such as DEFRA and MI5.
However, chasing an opportunity to progress my management career, I ended up back in main-stream construction with national electrical company who provided excellent experience in managing a cost centre as if it was my own small business, with a side flavour of FTSE 100 company politics and power.
Once I had exhausted the progression opportunities, having made some serious money for the companies share-holders, I was left with an appetite to make something for myself so I partnered with another Mechanical Engineer to help him build his business from his home-office to a serious local contender.
Whilst working for yourself is some of the most fun you can have at work, it’s also some of the most stressful and risky, and when my daughter was born I had to change my priorities. Splintering from the main business, I followed an independent path which has provided a lot of flexibility to be with my family when needed but also required the biggest change in my career yet – becoming a domestic plumber.
In some ways this is like starting right at the bottom of the construction industry again, but in reality, for me it is actually completing the full suite of experience. I use my apprenticeship skills of estimating and document management, my engineer skills in designing and trouble-shooting mechanical systems, my management skills in sales and cost control, and I’ve now added extra skills in accounting and pipe-fitting. However, I still don’t do much technical drawing.
Commentaires